Reduce unplanned downtime
Catch issues early and address the biggest drivers of downtime slowing production.
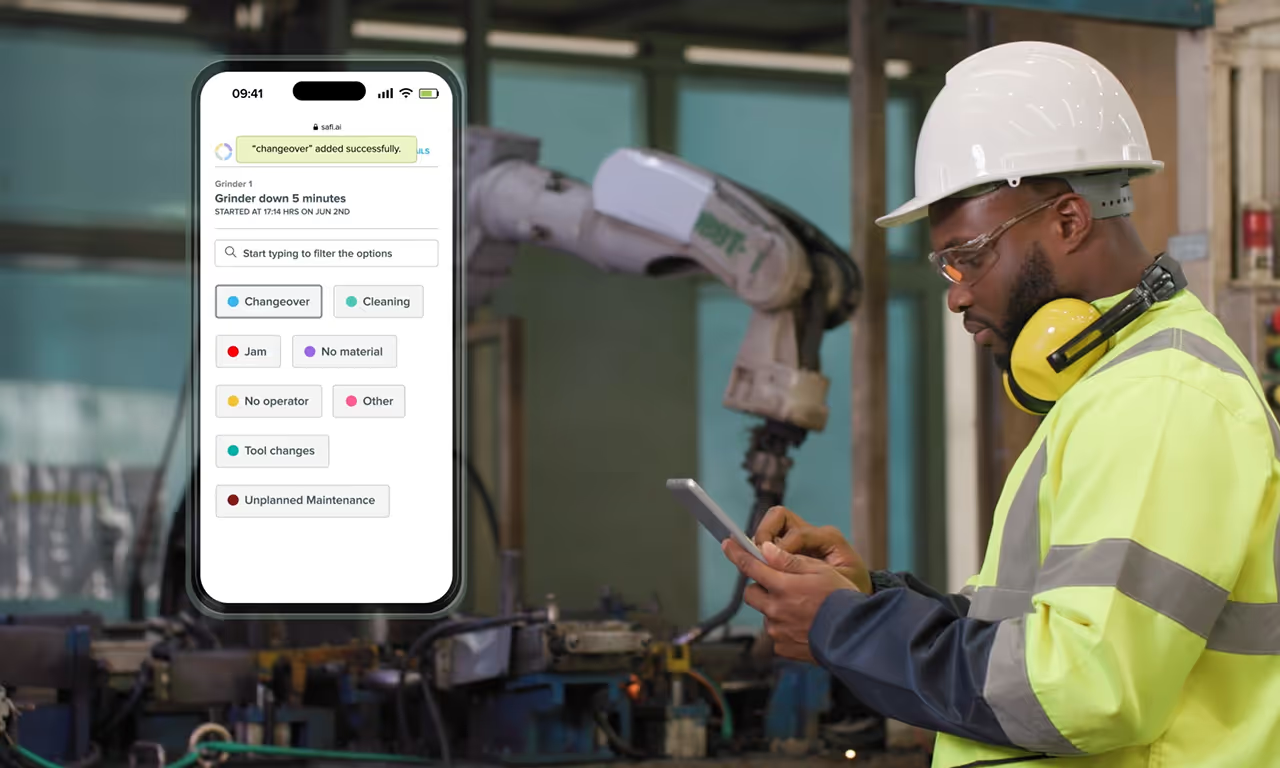
Trusted by hundreds
of leading manufacturers
From unclear issues to instant insight
Too often, downtime goes unnoticed until hours, or even shifts, have been lost. When you can’t see exactly when machines go down, unplanned downtime piles up fast.
Guidewheel gives your teams real-time visibility to catch problems early, identify root causes, and take action fast, keeping your lines running and producing more.
Keep machines up and costs down
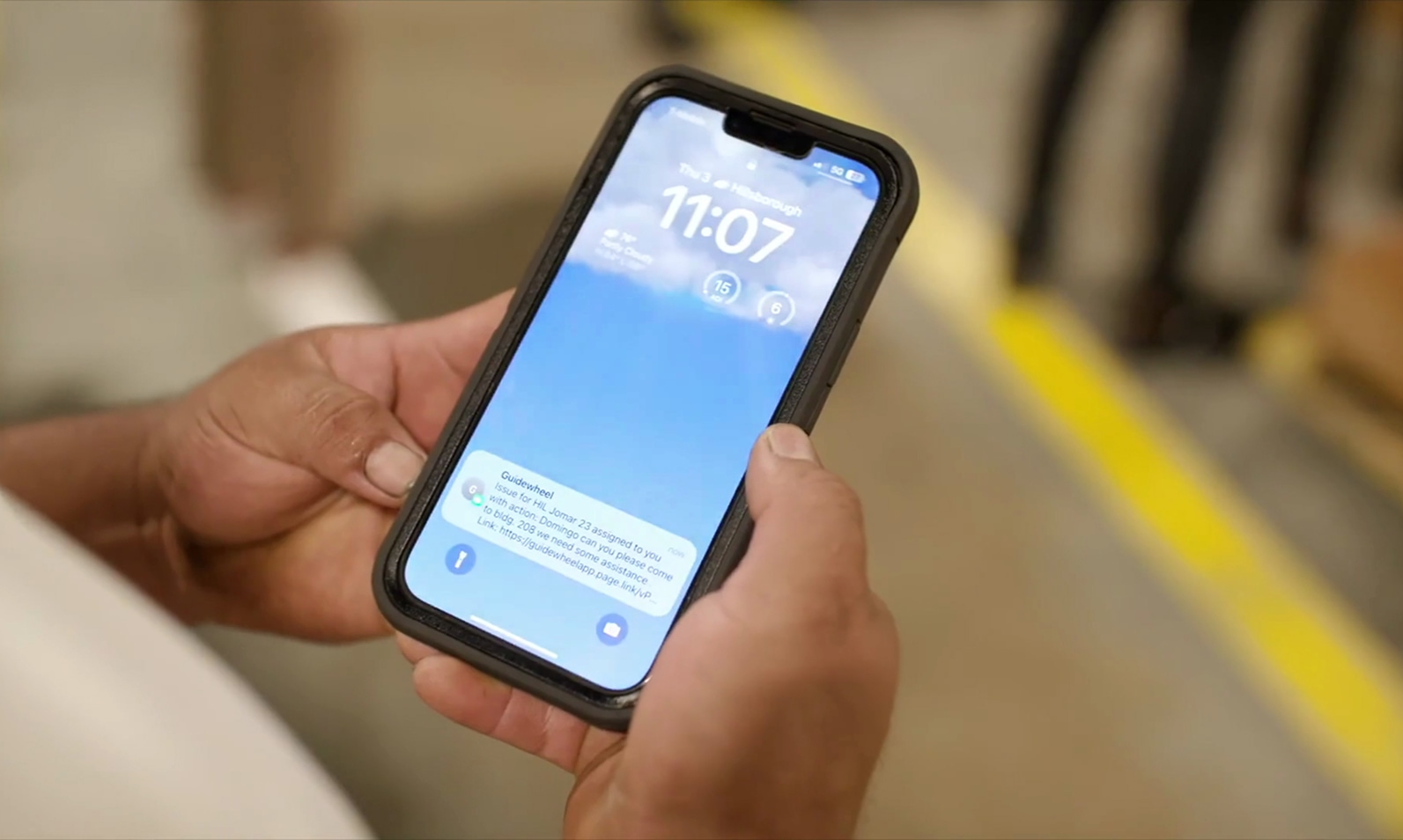
Respond faster to downtime
Get alerts and real-time visibility into downtime so your teams can respond quickly, without waiting on shift or weekly reports.
Focus on your most costly issues
Zero in on your top downtime drivers by machine, shift, or issue type, and direct resources where they’ll have the biggest impact.
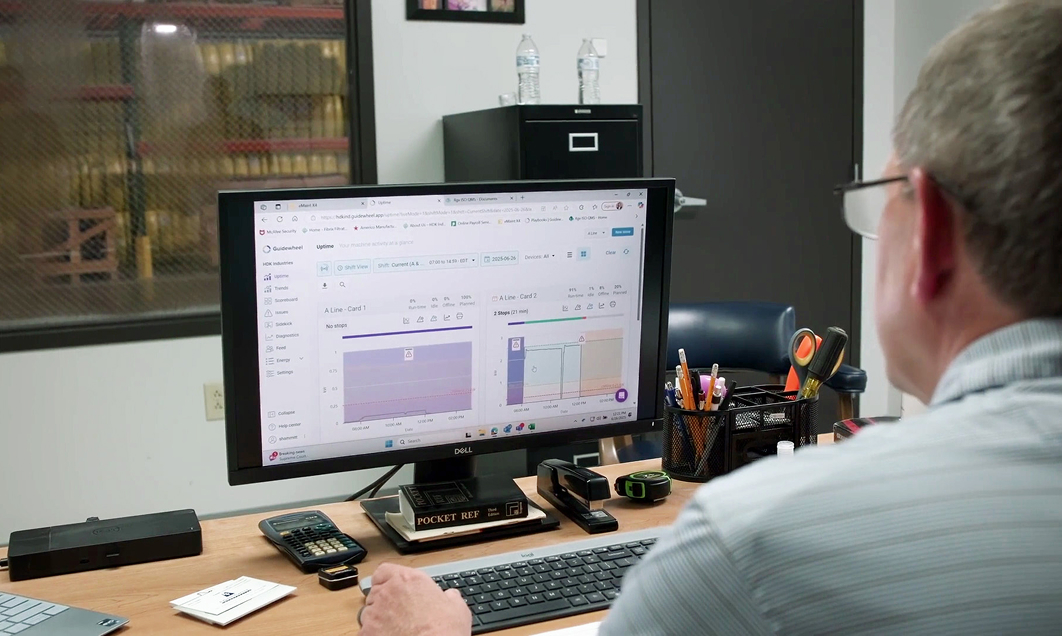
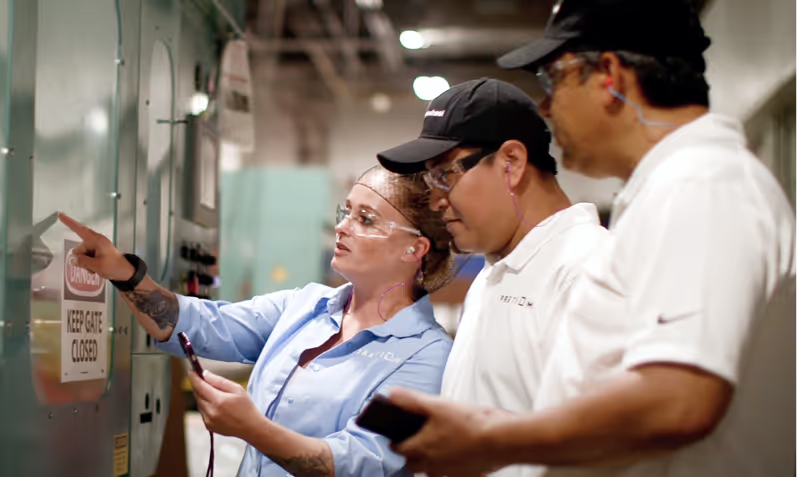
Recover hidden downtime
Identify and eliminate costly delays like slow changeovers, late starts, and microstops, that add up over time.
Lay the foundation for predictive action
Track downtime in real time today and be able to scale with AI, condition monitoring, and integrations to stay ahead of failures tomorrow.
.avif)
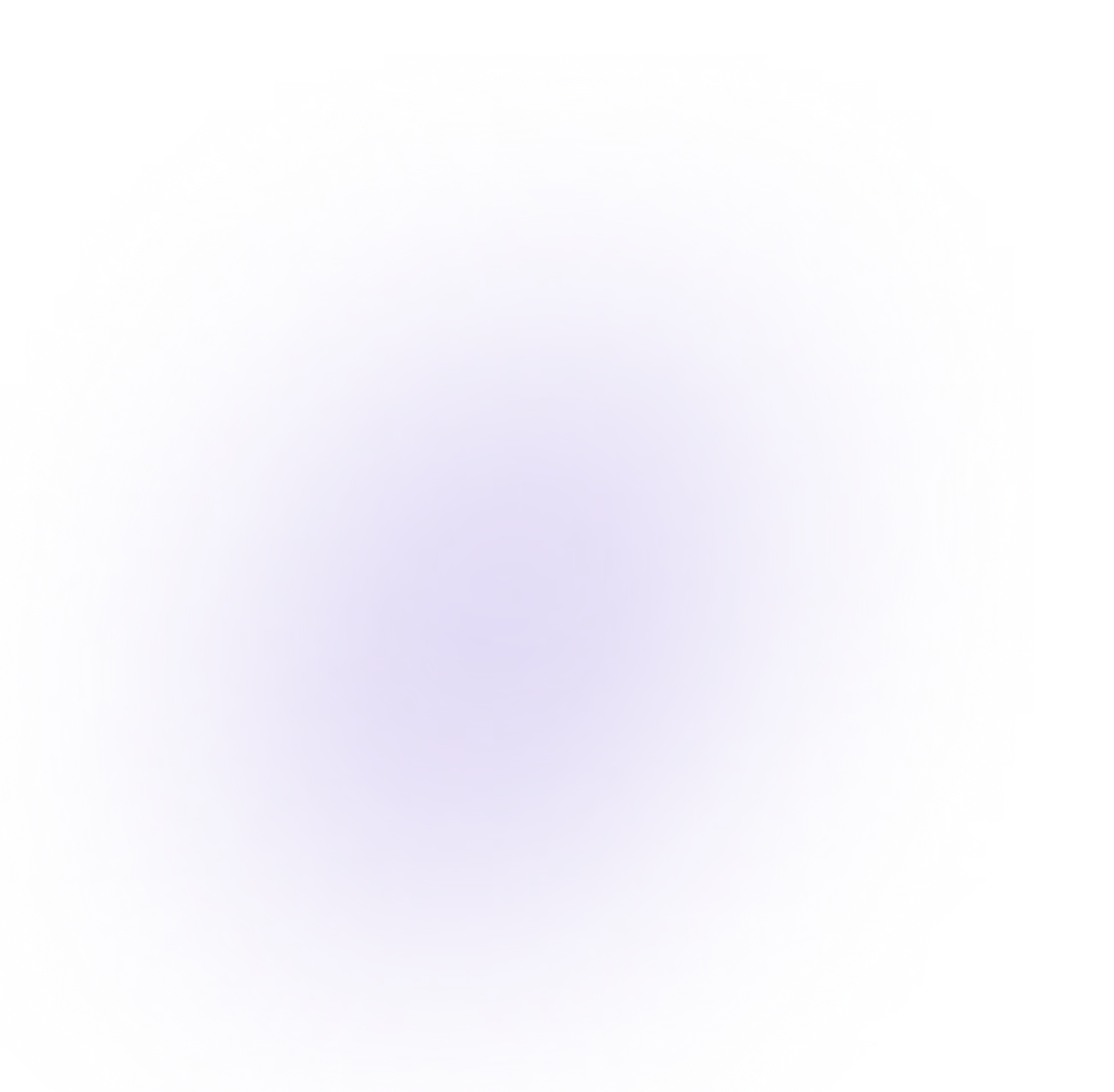
92% uptime achieved annually at Fibrix
Real-time visibility into downtime and machine performance through Guidewheel helped the Fibrix team resolve key issues, align their teams, and achieve over 90% uptime for an entire year on their most critical line.
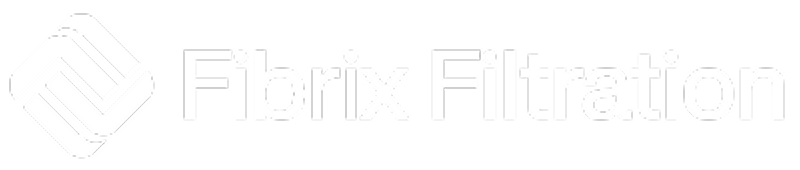
Scoreboards
Get complete visibility into factory performance across every line, shift, and site. Guidewheel’s scoreboards surface key metrics in real time, so your teams can stay aligned, act fast, and stay on target.
- Live dashboards with views at the machine and plant level
- Updates in real time across all shifts
- Display key metrics like runtime, OEE, and more
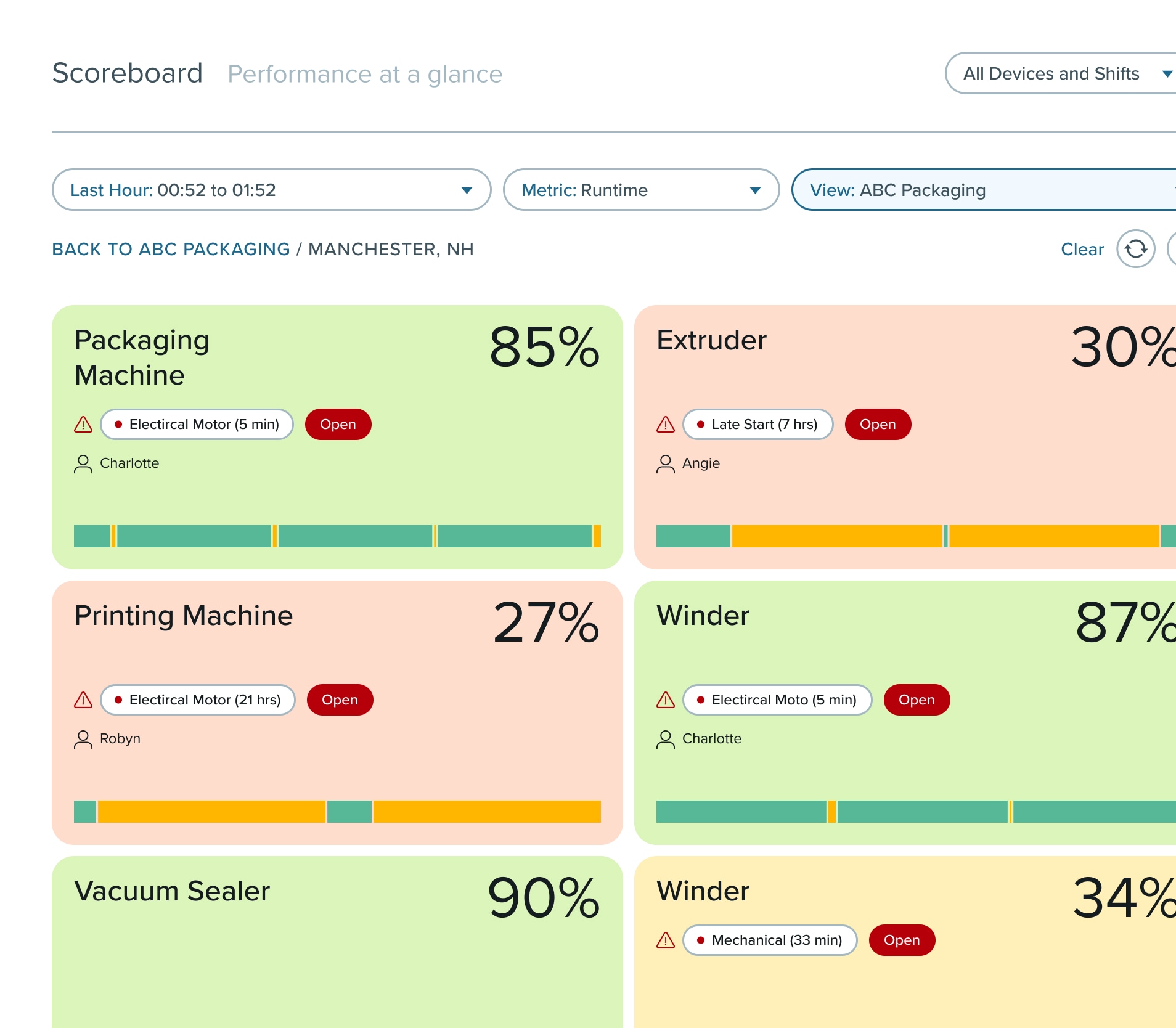
Uptime View
Monitor whether machines are running, idle, or down, and why. With real-time visibility into runtime, your teams can jump on issues before they impact production.
- See live machine status from any device
- Know duration and reason for all downtime events
- Spot and resolve issues as they happen
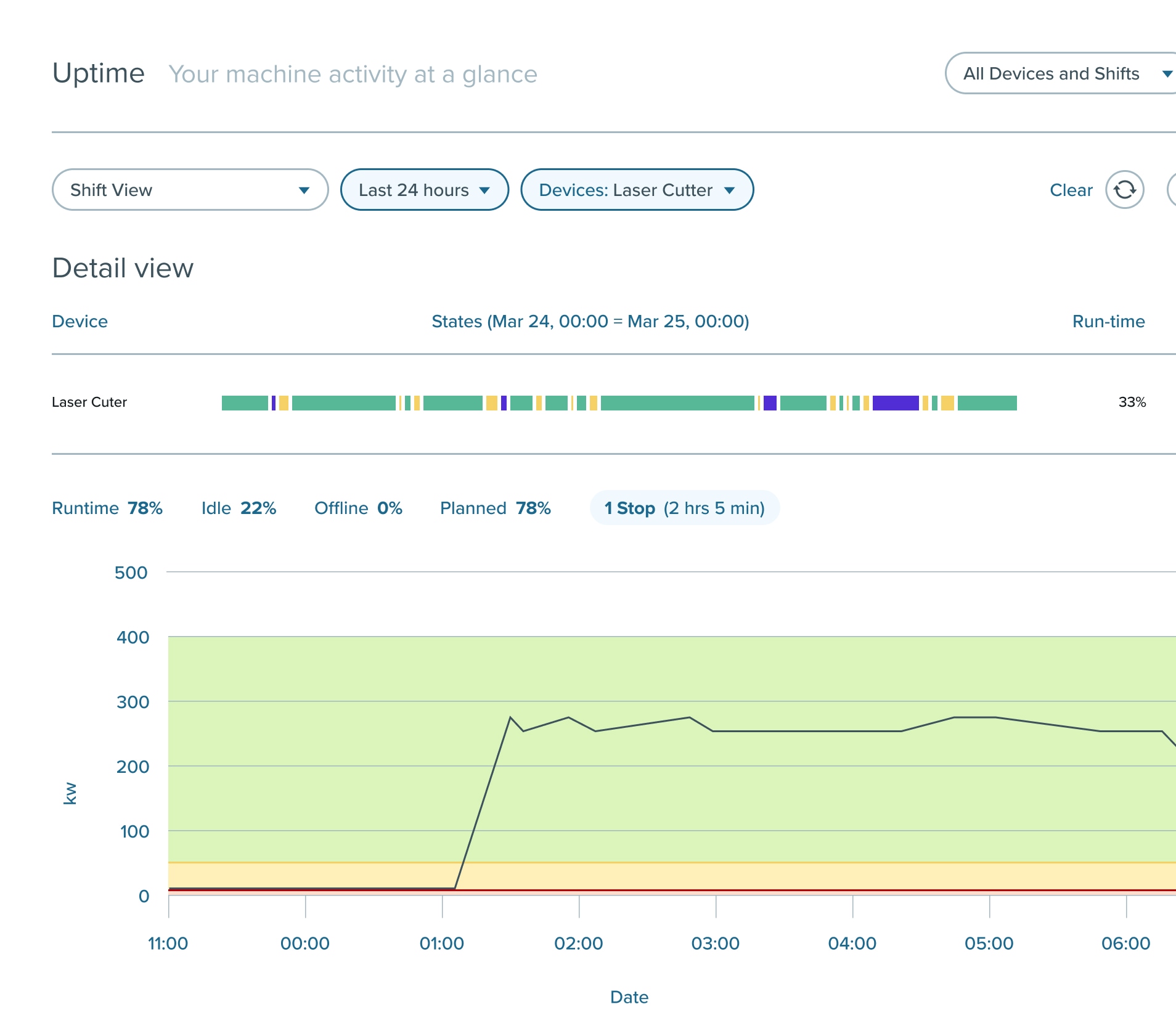
Mobile Alerts
Ensure your teams are instantly notified when downtime, overloads, or anomalies occur, no matter where they are.
- Detect downtime or performance drops in real time
- Alert the right person instantly
- Keep output steady across every shift
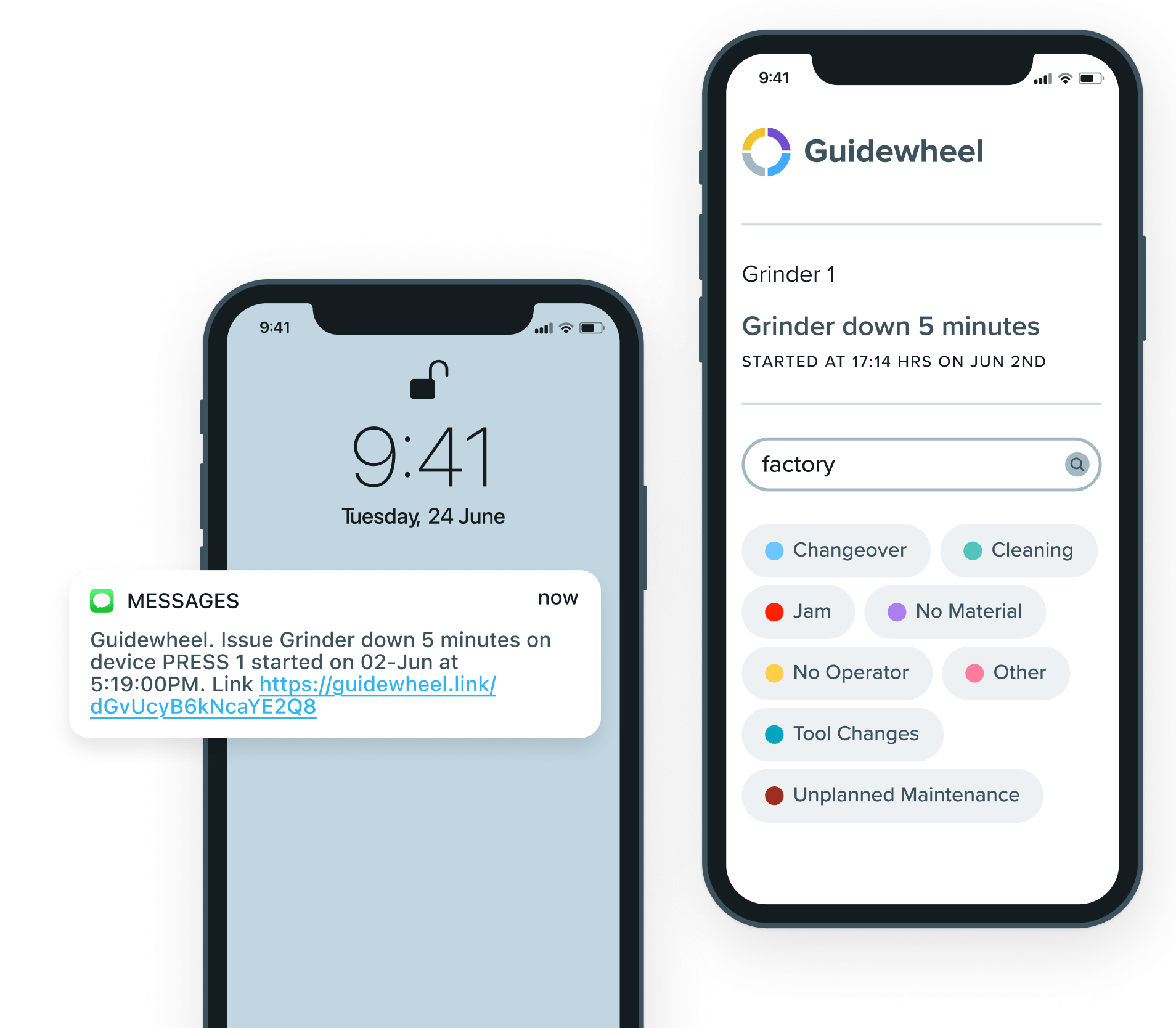
Operator Dashboard
Give operators the tools to flag downtime, log issues, and keep lines moving in real time.
- Tag downtime events and request maintenance support in just a few taps
- Record scrap reasons without slowing down production
- Feed real-time insights from the floor directly into your team’s decision-making
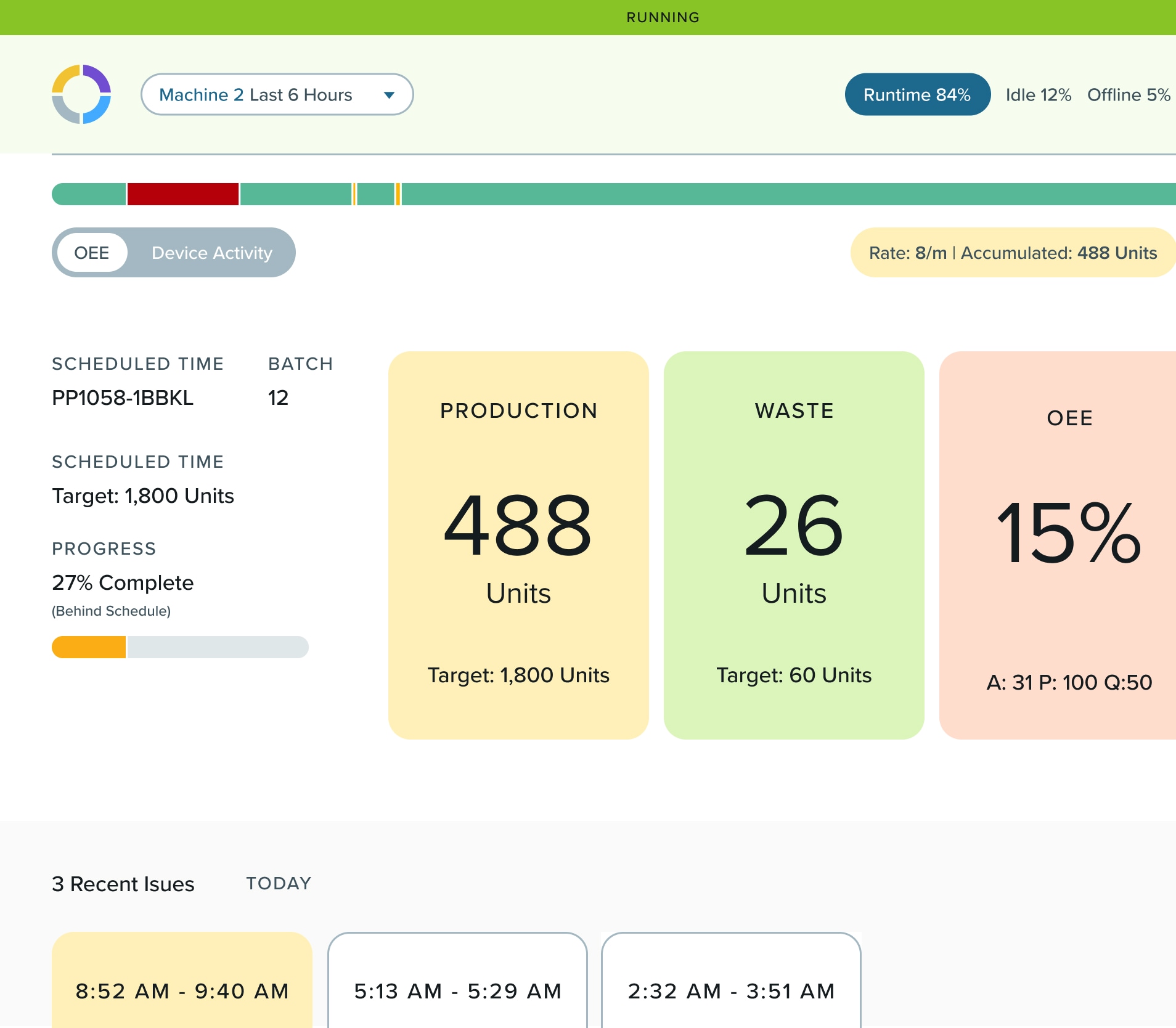
Pareto Analysis
Pinpoint and address your biggest downtime drivers to focus resources where they’ll have the most impact.
- Identify top downtime drivers by machine or type
- See which problems are costing you the most time
- Prioritize improvements based on data, not assumptions
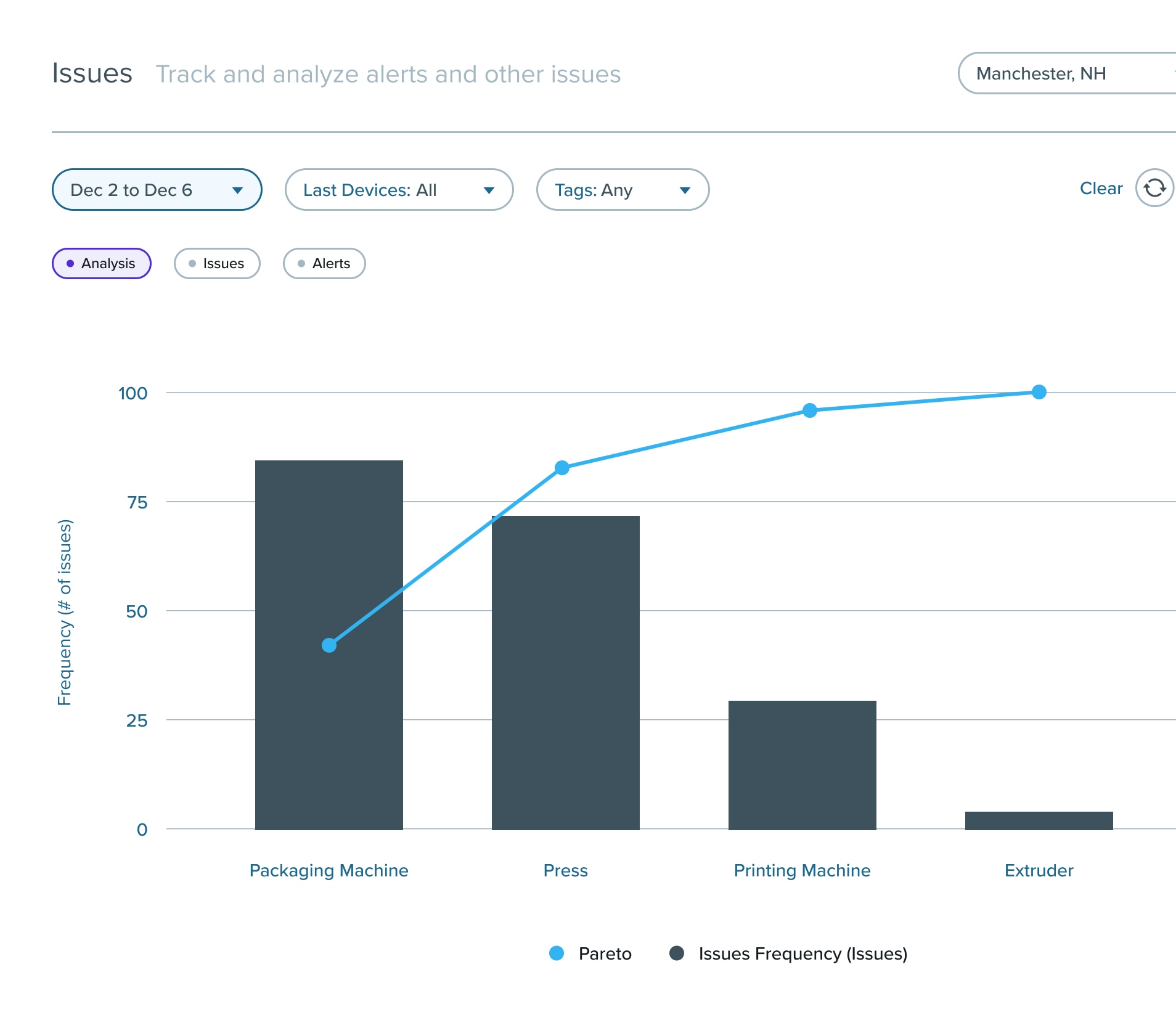
AI-Powered Anomaly Detection
Catch abnormal machine behavior before it leads to a major failure.
- Detect subtle deviations from normal performance patterns
- Surface potential issues that manual checks may miss
- Take preventative action to avoid costly unplanned stops
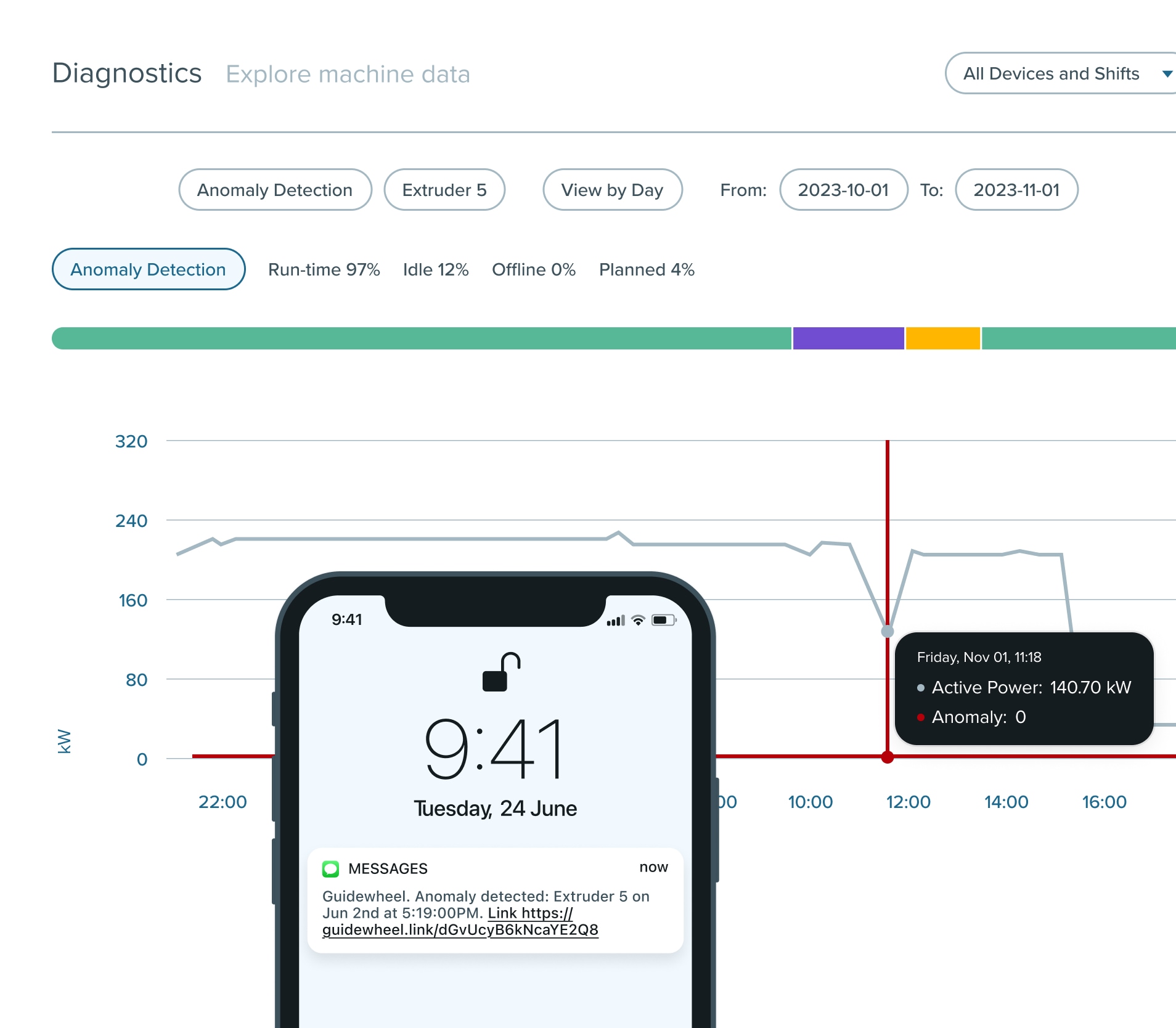
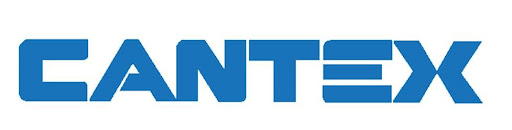
Frequently Asked Questions
Our sensors track real-time power usage to determine whether a machine is running, idle, or down. You’ll get instant alerts and visibility when the machine’s condition is down.
Yes. Operators or supervisors can tag downtime reasons with just a click, and reports surface trends over time so you know what’s driving losses.
Guidewheel works on any machine that uses power, regardless of age, make, or model.
Most teams are up and running in a day, with visibility live within hours of sensor install.
Ready to start reducing controllable downtime?
Let’s talk about how Guidewheel helps you catch issues early, take action fast, and keep your lines running smoothly.